Download White Paper: Lean Warehouse Aisle-Bay-Level-Position Bin Location Coding
Abstract
As we implement Lean Warehouses at numerous Clients, we are finding a multitude of bin-location coding schemes; the code that locates parts in aisles / bays / levels / shelf positions. As we’ve been to many warehouses, have seen different ways of coding, and came up with some of our own. This white-paper will discuss what is important when setting up location codes and some options based on the nature of your warehouse and distribution business.
Floor-Stock, Shelving, Racking
Before we explain these options… most bin location coding schemes are based on racking and shelving, assuming a relatively uniform warehouse layout (uniform racks going across the entire warehouse). This is not the case for many of our Clients, who use a combination of floor-stock, shelving and racking.
Floor-stock, in particular, is ideal for items that are uniform and stack well. This type of storage has no “levels” and “positions.” It is the densest way of stocking if you have a good way to grab items from high up and if first-in-first-out (FIFO) is not important. Make sure your bin location coding scheme works as well for floor stock as for racking and shelving.
Aisle Numbering
Aisles are usually, or we recommend, using numbers. We prefer to start with only even numbers (2, 4, 6…). If a future small modification adds an aisle, it is easy to fit into the existing aisle numbering scheme. Our number is therefore coded as 02, 04, 06, etcetera. Note, if you will have 50 or more aisles, you will need to add a digit; 002, 004, 006 as you will reach 100 or higher in your aisle numbering.
Additionally, you can “sectionalize” aisle numbering, using a section of numbers for different types of storage.
01 – 20: Small parts shelving
30 – 50: Floor Stock
60 – 80: Racking
This type of sequence will create zones, which most warehouse management systems (WMS) do, but without having to look at the scanners. Note that we leave open numbers between the different sections to allow for growth.
Bay Codes
There are three considerations for bay coding; alternating sides, letters or numbers, single or bi-directional aisle picking paths.
Alternating Sides
We recommend alternating sides (A on one side – B directly across or 01 on one side – 02 directly across) so the Picker will be naturally routed to pick from their right and left as they travel down the aisle.
Lettering or Numbering
You need to choose if you want to use lettering or numbering. Letters create a natural “hyphen” or break when you are looking at positions. “02/A” is more intuitive than “02/01”. However, if your aisle will have more than 13 bays and you are alternating sides then with letters you will need to go to AA, AB, AC, etcetera. It is much more intuitive to have 01 – 99 as your bay numbering than changing using two-digit letters.
Single or Bi-Direction Aisles
If the nature of your pick operation is you are gathering many items or many orders on one pick path then you probably will use single-direction aisles. These warehouses do not have a steep velocity curve (V1 = items with the most “picks”, V4 are items with least “picks). It is likely the Picker will have to route through much of the warehouse or zone to pick the items for their orders.
Shelf Level
There are two choices for coding shelf height, numbering or the shelf-height in inches, or centimeters.
Numbers are what is most widely seen in warehouses. There is a logic to the bottom shelf being “1” and the top shelf being a larger number. Note, you should always make the lowest level “1” not zero. We have always found it more logical for the first level to be number 1. In addition, this makes floor stock “level” codes the same as an item on the floor level of a rack or shelf. In addition, always number from the bottom up so you can add shelves without having to reset your shelf level numbering scheme.
The other option is using the shelf height in inches or centimeters. There are two advantages to this design. First, you can easily add shelf levels without having to reset shelf levels for the bays that get the additional shelving. Second, the Picker can easily look at the location of the item and know if he/she will need equipment to reach an item higher up on the shelf or rack.
Shelf Position
Some organization prefer to add positions to their shelving. We don’t recommend doing this as this can change if items need more shelf space and it is easy for one item to cross over a specific position and be in two positions. These codes are usually letters, A, B, C and D.
Examples
Below are some visuals to help you see different schemes. Of course, as we are implementing Lean Warehouses, every facility has some level of uniqueness due to the nature of the product, the size and shape of the building or the function of the building (sharing the space with manufacturing).
We can support you as you implementing your Lean Warehouse. Email info@supplyvelocity.com to connect with a Lean Warehouse Specialist.
Single-Direction (Snaking) Aisles – Number for Bay / Number for Shelf Height
Figure 1 below shows the top-view and elevation-view of a warehouse that uses single direction aisles. This layout supports when a Picker will route through most aisles, picking orders with many items. This design can be ideal for companies without a warehouse management system (WMS) that creates pick-sequence other than smallest to largest. It also can support picking from paper versus being guided by a scanner
Bin Location Example: 02 (aisle) / 01 (bay) / 3 (level) / C (shelf position)
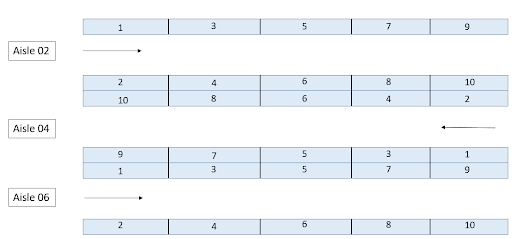
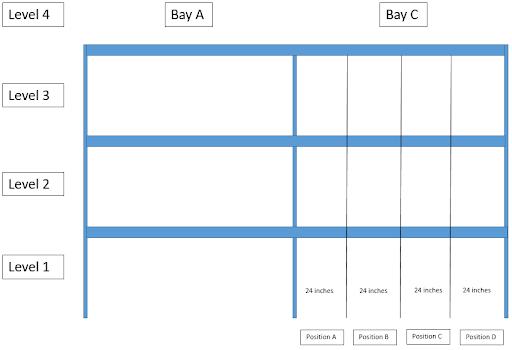
Single-Direction (Snaking) Aisles – Letter for Bay
Figure 2 below is identical to Figure 1 above but uses letters for the Bay code. This can be beneficial by creating a natural break in locating codes between aisles (number) and shelf level (number)
Bin Location Example: 02 (aisle) / A (bay) / 3 (level) / C (shelf position)
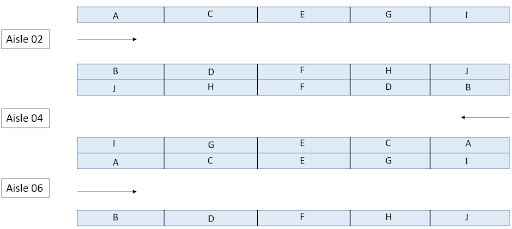
Bi-Direction Aisles – Number as Bay
If your picking is unlikly to require snaking and aisles can support two-way travel, then coding all bays from left-to-right or right-to-left has a significant advantage. When all bay codes go in the same direction it is easy to know where a bay is located across the entire warehouse. This can be advantageous for identifying where cut-throughs are located. This is shown in Figure 3 below.
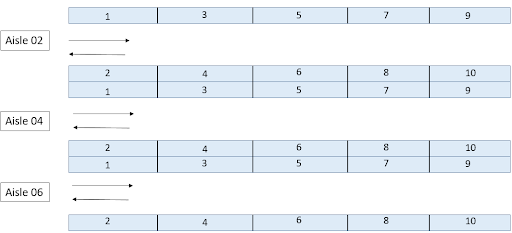
Shelf Level in inches or centimeters
As mentioned above, setting your shelf or rack levels based on their actual height has many advantages. Below in Figure 4 we show how levels can be coded based on height.
Bin Location Example: 02 (aisle) / A (bay) / 048 (level) / C (shelf position)
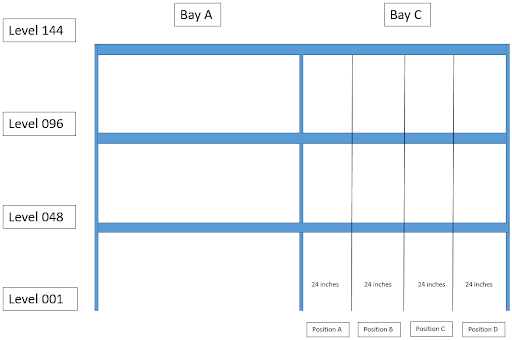
Mitch Millstein, Ph.D.
Supply Velocity, Inc.
mitch@supplyvelocity.com
(314) 406-4962
November 2021
Ask us your Lean, Six Sigma, or Supply Chain question.
We’re the experts! We’ll get back within 48 hrs. with a valuable response.
"*" indicates required fields
“Mitch Millstein and his team helped guide our shop fabrication division in the re-layout of our custom pipe and steel fabrication facility when we moved into a new building. It is not only the results but how he helped. We were involved in every step. I personally did time studies and was able to see the non-value added steps required to manufacture in our old layout. When we created our new layout, everyone was involved, from the executive team to our direct labor force. With Mitch’s help we increased our throughput by a 3x multiple, while providing more competitive prices to our clients as a result of the efficiency improvements.This has enabled us to not only make more money but also to expand our commercial reach and serve more, and larger customers. I would recommend Supply Velocity to any company that wants to make improvement in supply chain and operations.”
“We used Supply Velocity to rethink our sales process. By analyzing the entire process we found wasted time in our Sales, Admin and Operations departments. Streamlining this process created extra time for each Sales Rep, allowing them to spend more time with Customers and increase the value we add. Gross profit margins are up 40%!We are now using Supply Velocity to help us rethink our entire Strategic Plan.”
“In 2015 we began working with Dr. Mitch Millstein to optimize our inventory locations supporting e-commerce and in-store inventory needs. From this work we developed a new omni-channel warehousing and inventory plan that entirely redefined our approach to warehousing, inventory management, store distribution and fulfillment. As a result of the analyses by Dr. Millstein we have begun the move to an improved omni-channel design by reassigning MSAs to new warehouses, greater leveraging of in-store inventories to satisfy e-commerce demands, and exploring acquisitions of new warehousing space in strategic locations. We have already seen an improvement of $300,000 from both more efficient shipping strategies due to better inventory management.”
“Supply Velocity gave us the tools to analyze our business and processes based on the facts and numbers versus our perceptions. Our common quote was “Let the numbers lead us”. The key for our organization was how quickly we moved from classroom to actual project initiation. We were able to jump in, start using the tools and see a difference right away.
The get-into-action approach was good for our culture.”
“Supply Velocity has helped Clean succeed in a number of ways. First, they provided the education that kicked off our Lean Process Improvement journey. They also facilitated a number of large supply chain and process improvement projects including: 1) building quality into our direct-labor productivity incentive program, 2) designing the layout of our garment warehouse, and 3) streamlining our route service process.We have integrated the methods that Supply Velocity taught us into our management and strategic planning. In the process our quality measurement has improved 22% from 2013 to 2015, we have reduced required annual labor by 2200 hours from the garment facility layout project and we’ve seen 50% decrease in error rate. Obviously the numbers speak for themselves, but just as important, Supply Velocity has been fun to work and have become true partners. They have “taught us how to fish” so our internal teams are able to implement change on their own, with the skills we learned from Supply Velocity. This relationship has been invaluable.”
“Supply Velocity has provided the technical expertise and political capital to move our project forward. They have just the right amount of push and the right amount of support. Supply Velocity has helped us make real changes to improve efficiencies in logistics without jeopardizing our performance. We’re happy and our customers are happy.”
“Your process encourages this group to work together, better communicate and have fun doing it.”
“Closure Medical recently completed a major reorganization in order to enhance our ability to rapidly create innovative medical devices. We hired Supply Velocity to help us map out the process and service flows of the new organization that would maximize our product development process (PDP). In four weeks, Supply Velocity helped us envision a new PDP structure, develop measures and accountability for each step, and gain consensus within the organization. Supply Velocity’s focus on speed and accountability helped us complete a critical project in a timely fashion.”
“For several years we have worked with Supply Velocity to support us with their expertise on Lean Operations and Supply Chain Management. Supply Velocity has helped us implement Lean, improve our inventory systems, and educate our people. They are professionals who are always available to help us as needed.”
“The role of the Erie Insurance Marketing Department has been evolving over the past several years – from a support role to a more critical role of driving growth in our organization. Because of our increased workload and desire to prioritize the most critical projects, we hired Supply Velocity to teach us the skills of Lean Six Sigma.Participants included the Promotions, Market Research and Agency Licensing sections of the Marketing Department.
We learned valuable tools to help us to prioritize based on the voice of the customer.
I firmly believe these skills made a difference in how we work every day. We are moving new projects forward, eliminating or changing ineffective processes, and we are a much stronger department. We continue to use the tools to help us with our highly-complex and time-consuming projects. Supply Velocity helped us to accomplish our goals.”
“Isolating a problem, finding short, and long term solutions with measurable results is what was promised and results is what was delivered by Supply Velocity. Upon launch of the Lean Six Sigma Selling System, we knew more about our customers, our products, and were able to create a solid plan to increase sales of our most profitable products. Within months of implementation, our booked sales jumped 60% and our most valued customers were getting direct, active, and calculable attention.”
“Anheuser-Busch Precision Printing had been implementing Lean Operations on our own for the past two years. We needed to move faster and partnered with Supply Velocity, Inc. Through Supply Velocity, Inc.’s mathematical workflow balancing and visual management tools, dramatic improvements were achieved. The entire converting operation was rearranged based on Lean principles. The result is a 20.6% productivity improvement, enabling us to operate with 23 fewer people in production.”
“Myerson engaged Supply Velocity, specifically Ray Davis to visit our plant in Trinidad to conduct a two day assessment of our production procedures and provide us feedback on areas for improvement and where applicable, areas for future analysis.Put simply, we got everything we paid for and in addition to more in depth analysis, we got specific tasks that were immediately actionable. Our local management team found Ray to be engaging, highly credible and insightful based on his wide experience. In other words the cultural differences and lack of specific industry knowledge weren’t impediments to things we could implement immediately and on our own. In a nutshell it was money well spent and will pay itself back many times over.”
“I am thrilled to provide this testimonial for Supply Velocity and their outstanding work in implementing Lean Warehouses and processes at Crescent Parts & Equipment through the COVID pandemic. With their data-first focus and Mitch’s exceptional coaching and experience, they transformed our business into a more supply chain-oriented organization, enabling us to grow while prioritizing employee safety and creating a better work environment. Supply Velocity’s expertise in Lean methodologies and their comprehensive evaluation of our customers have been instrumental in optimizing our operations and increasing customer satisfaction. We highly recommend Supply Velocity to any company seeking to implement Lean processes and enhance their supply chain efficiency.”
“Supply Velocity created visibility within our Assurance Services Group… visibility of performance, Client-service, employee satisfaction and processing time. Using the Supply Velocity System, Audit Report Cycle time is down over 50%. We are using his strategies to create greater Client loyalty.”
“We are using Supply Velocity’s Lean Six Sigma methods to analyze a variety of processes including rationalizing SKUs (stock-keeping-units). By using math to evaluate SKUs we took some of the emotion out of our decisions. We expect significant increases in sales and productivity from reducing poor performing SKUs.”
“In thirty years of hiring consultants, Supply Velocity, Inc. was the first to tell me what they were going to do, set a price they stuck to and substantially exceed my expectations. I have recommended them to friends and acquaintances. They were true partners in assisting with the turnaround of an acquisition we had been struggling with for two years.Their math-based technology, solid down-to-earth facilitation skills, and positive, patient and enthusiastic attitude combined to make our implementation of Lean a very rewarding experience.
We increased our production by 50% in the first month of implementation and continue to see improvements. Improvements have not only been realized in productivity, but also in quality and morale. We have increased profitability by $2M on flat sales of $10M.
Based on Supply Velocity, Inc.’s integrity and our results, I will continue to refer them to others and utilize them in the future as we expand our company through acquisitions.”
“Our experience with Supply Velocity was one of the best values we have ever had from a consulting project. Cyril Narishkin brought a structured lean methodology, invaluable experience and engaging facilitation skills to help us streamline a very complex and disjointed sales order process. Just as importantly, our team now has the knowledge and process competencies to address other business improvement opportunities going forward.”
“Supply Velocity is driving instrumental change in our inventory management processes. This is critical for us to be competitive in a supply chain environment with numerous disruptions. They are making change happen, which can be challenging in a 182 year old organization.”
“Supply Velocity’s Lean Six Sigma System has given us new tools to help improve our sales performance. We have learned new ways to analyze our business which makes problem solving more accurate and has made us better leaders.”
“In a time of volatile supply chain disruption, Supply Velocity is helping us develop Demand and Supply Planning processes to proactively tackle these new challenges. They are genuine partners, working with our team, facilitating and teaching.”
“Many thanks to all three Supply Velocity presenters. I think you guys took a very difficult time for learning and capitalized on everyone’s time and training needs. I truly hope this helps your business as this was a considerable undertaking on the part of Supply Velocity. Outstanding!!”
“In the spring of 2003, the St. Louis Area Chapter of the American Red Cross engaged Supply Velocity, Inc. to perform a study and make recommendations to streamline office processes, maximize cash flow in purchasing and warehousing and restructure and enhance our maintenance department. Supply Velocity, Inc.’s process was methodical, flexible, staff-oriented, inclusive and, above all, trackable.In the last six months, our Chapter has realized expense savings of over $380,000 annually, and significant improvement in intra-company service levels has been attained. Supply Velocity, Inc. will return to the Chapter periodically throughout the next 18 months to audit our newly implemented processes. We have been pleased with our results and Supply Velocity, Inc.’s professionalism.”
“C&R was struggling with labor productivity. The construction crews were often missing materials that they needed to do their work. This caused significant idle time. Supply Velocity, Inc. and C&R used value stream mapping and visual management tools to make dramatic improvements in operations. Most importantly, two years later C&R is sustaining and improving on the implementation. C&R’s return on investment was 11:1. C&R had a record year last year in both sales and profits and would not have been able to pull it off without the changes Supply Velocity, Inc. helped us make.”
“We are pleased that Essex selected Supply Velocity, Inc. as our Lean Implementation Partner. At one facility, we have saved over $350,000 in work-in-process inventory, reduced throughput time from 2 weeks to minutes and increased inventory turns 3 to 8 times per year. All these results are in just 6 months. Our return of investment is very high.”
“We used Supply Velocity on our Warehouse optimization project. One of the key characteristics of Supply Velocity is that they listened to our requirements and provided a clear path for our Warehouse processes using lean tools and our future sales growth as objectives.”
“We engaged with Supply Velocity to help us embed process improvement at all levels of the business. Our team learned from Mitch to let the data drive decisions, to use Lean tools to help us see our processes critically and objectively, and to create a control plan to manage all of the tasks that were the outcome of the data study.The project turned out to be very significant to the company and most importantly, our customers. We reduced our customer wait times by 40%, and cut in half the labor cost to fulfill customer orders.
Some results are not able to be measured. However, as a result of this project, we have started to build a Lean mindset and culture, which is part of our strategic mission to save our customers money. Supply Velocity has been a valued partner in this mission.”